Our integrated process control system connects the workforce, activities and equipment in real time.
That enables an automatic production scheduling system that reacts to disturbances in seconds.
One of the top challenges in modern mines is the manual coordination of the vast number of possible interdependent activities. Manual scheduling is a hard and arduous task, performed as in a continuously unpredictable unpredicted changing environment. Today, our work order distribution and reporting are done using radio or face to face meetings between the shifts. Without real-time information about the status of mobile equipment or tasks, mines struggle are inadequate unable to react timely and accurately to deviations. This reduces operational efficiency and increases costs.
Today mines are getting more and more wireless coverage. This enables instant updates of the plan to the underground operators and the latest task progress information can be sent to the scheduling system. This closed-loop feedback can be used for both the task and maintenance planning and this will reduce the burden of planning for the operator and this will result in higher quality of the inputs and less stress on the people as well as improved efficiency and increased yield.
Many challenges arise when working at the forefront of technology development. One challenge for the control system pilot has been to integrate a new auto scheduling product with the existing customer manual planning tool without causing any production disturbances or loss of valuable production data. The tight collaboration with the operators in the mine will guarantee a smooth transition and leverage the full potential of the pilot.
Automated scheduling and progress reporting allows mine operators to monitor and review mining activities based on targets, metrics, and KPIs. Variances are highlighted so operators can take appropriate actions. In addition, the system allows mine planner to optimize resource usage in real time and follow the production plan more effectively. With the integrated control system in place, mining companies can improve responsiveness to unplanned events, increase efficiency and improve safety in the mine.
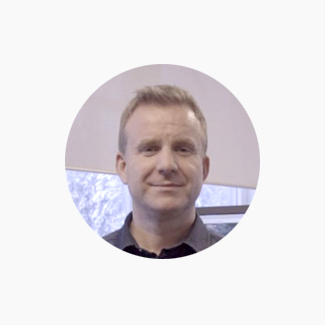
Rickard Lindqvist
R&D Senior Project Manager, ABB
A project like this has been a long term dream of mine. It is really exciting to make the project together with great colleges and partners.
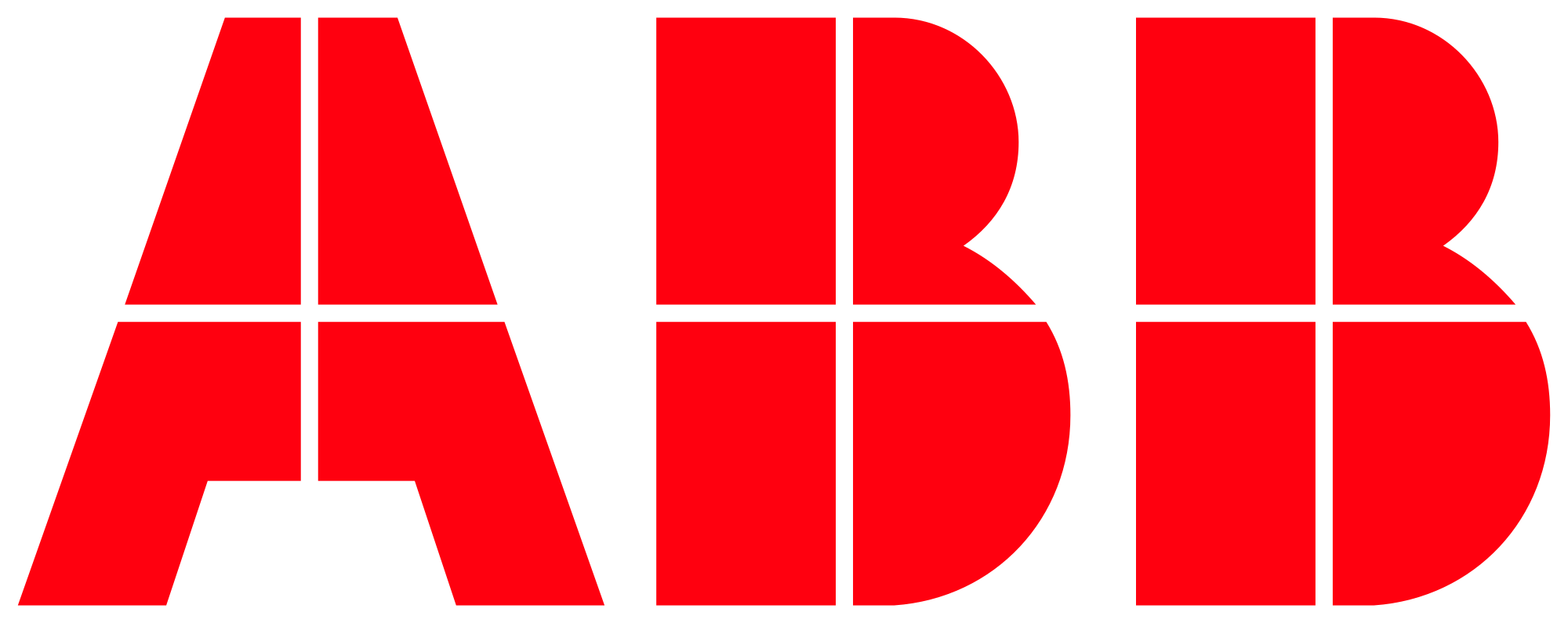
The Virtual Mine – a digital twin of the mine in a computer environment
A powerful tool, in which different scenarios can be evaluated, and once a good solution is found, it can be implemented in the real mine.
The Virtual Mine has been done to develop a digital twin of the mine in a computer environment. In the Virtual Mine, a user can conduct and perform analyzes of the effects that changes will have on the operations in the mine, either in present time, or in a future scenario. This creates a powerful tool, in which different scenarios can be evaluated, and once a good solution is found, it can be implemented in the real mine.
The Virtual Mine is also connected with the ABB scheduler, which is a tool that is able to create a schedule for the equipment in a mine, and respond to changes and status updates from the equipment, so the schedule can be adjusted. When the Virtual Mine is connected to the scheduler, it feeds the scheduler with production requests, and also acts as the vehicles in the mine, to receive work orders from the scheduler, as well as reporting back status updates, disturbances etc. This makes it possible to evaluate long-term effects for scheduler algorithms as well as improving the quality within the scheduler. Both aspects of the Virtual Mine, to analyze changes, and to evaluate and improving the scheduler can be done without disturbing the day-to-day operation in the mine.
A major challenge has been to use the ABB scheduler together with the Virtual Mine, which runs in a non-real time environment, where the Virtual Mine can simulate the mining operations during multiple weeks in a matter of minutes.
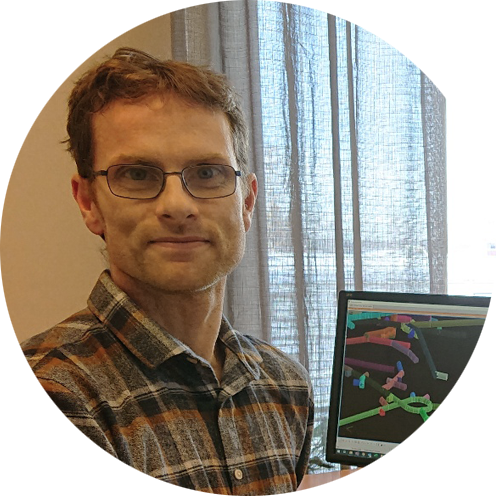
Fredrik Sundqvist
LTU